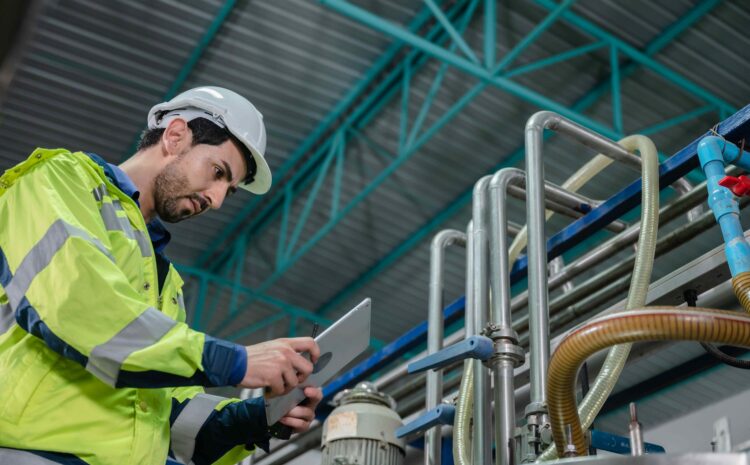
SERVICES FOR HYDRO TESTING AND PRESSURE TESTING
Whitewater is a leader in the design, installation, management, and operation of hydro-test water supply systems for hydro-testing API 650, 620, and 653 storage tanks, as well as AWWA storage tanks, pipelines, and ASME pressure vessels.
We have over 250 years of combined expertise in Canada’s water management and hydro-testing sectors, and have developed methods and procedures to meet our clients’ unique demands and situations. We operate year-round and are capable of functioning in extreme cold weather thanks to our unique heating equipment and extensive cold weather operating procedures. Additionally, we are able to operate in remote and environmentally sensitive places due to our systematic methods and procedures that minimize environmental effect and comply with federal waterway regulations.
HYDRO/HYDROSTATIC TESTING
We provide hydrotesting services for storage tanks of all sizes and types, including new construction and re-certification of existing storage tanks. We provide comprehensive hydrotest services, including obtaining crossing agreements on public and private land, obtaining diversion licences from applicable regulatory bodies, installing permanent or temporary water pumping systems, particulate filtration, water sampling, and conducting code-specific functional tests on the storage tank in accordance with applicable construction codes or standards. Our services conclude with the provision of a professionally produced turn over package that includes all of the information necessary for the appropriate regulatory body or utility commission to give the fit for service authorization.
This hydrotest is not only designed to identify leaks, but also to offer the customer with a complete operational test environment for purposes such as foundation settlement, rolling ladder operational check, or floating roof pontoon leak test and operational run through. Our highly qualified technicians and project managers are trained to safely and professionally assist all aspects of the test operations.
As with all of our services, our methods and procedures have been created with the utmost care to minimize our environmental effect.
Additionally, we support hydrostatic testing necessary for various goods such as pipes, spheres, and ASME (American Society of Manufacturing Engineers) Division 1 or Division 2 pressure vessels. This integrity test fills the vessel or pipe system with liquid and pressurizes it to a predetermined test pressure.
GET IN TOUCH WITH US
Contact us now for an estimate on your hydrotesting demands!
HYDROTESTING / PRESSURE TESTING
The objective of hydrotesting newly constructed API storage tanks is frequently misunderstood in the market. Many people feel that hydrotesting a newly constructed API 650 tank is just a leak tightness test, while others consider that hydrotesting is necessary for settlement measurement. Both are somewhat true, but highlight the discrepancy around a thorough understanding of what goes into hydrostatic testing a newly constructed tank.
Without delving into particular risk management recommendations contained in individual end user and owner requirements or into the exclusions or waivers contained within the API-650 Standard, the following are described as “the primary reasons for hydro testing a newly constructed tank”:
Ascertain that the tank is leak-free and secure, including nozzles, manways, shell seams, and attachments.
If a pontoon-style floating roof is built, verify that the pontoons are leak-free and the manway access is functional.
Ascertain that the weld integrity is sufficient to survive operating conditions
Permit consistent settling on the tank base to be confirmed.
Conduct a comprehensive functional test of all tank accessories, including rolling roof stairways for full range of operation and self-leveling functionality, floating roof drain range of operation, floating roof range of operation, floating roof seal range of operation, floating roof seal may be installed and tested for range of operation, anti-rotation devices, and so on….
In summary, hydrotesting verifies a tank’s fitness for service by performing an integrity test and reducing the danger of catastrophic failure by simulating operating circumstances with a test medium (water) with a specific gravity larger than that of the intended cargo. As a result, this hydrostatic test puts the tank to a more severe environment than it would encounter in regular operation. Additionally, additional testing stages such as uplift tests of anchor bolts and chairs may be added to a hydrostatic test situation when tanks are intended for increased internal pressures (lower than those specified in API-620) or when a tank is planned to operate in a seismic zone.